
From Screws to Filter Presses: Understanding Aggregates Dewatering Equipment Options
In aggregate processing, excess water content in materials can affect product quality, increase transportation costs, and create environmental concerns. Efficient dewatering reduces drying time, improves handling, and conserves water. Incorporating dewatering equipment such as dewatering screens, sand washing plants, fines recovery plants, fine material washers and filter presses can significantly reduce moisture content.
Understanding the capabilities and limitations of dewatering equipment helps producers optimize material recovery and minimize costs by choosing the equipment that is best suited for their operation.
The Role of Dewatering in Aggregate Processing
Dewatering is the process of removing excess water from aggregate materials to achieve the desired moisture content. This process plays an important role in aggregate processing as producers are looking for an efficient and economical way to separate water from solids. While water is an essential part of all washing operations, it is not desirable in the final product.
Dewatering in aggregate processing comes with several challenges, including effectively handling ultra-fine particles and slurry, which can be difficult to separate from water. Operations must focus on reducing the environmental footprint of wastewater by implementing efficient water management and recycling systems. At the same time, there is a constant need to balance water conservation with production efficiency, ensuring enough water is used for effective washing while minimizing waste and operational costs.
Despite the challenges that come with this process, effective dewatering also offers several key benefits. By removing excess moisture and fine particles, the quality of material is improved, resulting in cleaner, more consistent aggregates. Dewatering also helps reduce waste by recovering valuable fines and minimizing slurry disposal. Efficient dewatering lowers water consumption, promotes sustainability and reduces operational costs by recycling water back into the washing process.
Understanding the important role dewatering plays in the aggregate industry is key before evaluating the various types of dewatering equipment designed to optimize efficiency and material quality.
Types of Aggregate Dewatering Equipment
Dewatering Screens
Dewatering Screens are a versatile option for separating water from material. Dewatering begins when a slurry is fed onto the dewatering screen, where water rapidly drains, causing sand to accumulate on the screen media surface. Counter-rotating motors generate motion that moves solids toward the discharge end, while water passes through the screen. The combination of the screen media and a discharge weir forms a deep sand bed, which acts as a natural filter, retaining material finer than the screen openings.
Dewatering screens can be used in a wide variety of applications such as dewatering, desliming, rinsing, scrubbing, sizing, and more. They are most commonly used for dewatering washed sand and aggregates that require moisture reduction before stockpiling or transport. Dewatering screens are designed to handle materials, including sand, gravel, crushed stone, frac sand, and more, to generate a drip-free product.
Adding a dewatering screen after washing equipment can greatly benefit the operation by efficiently removing moisture and leaving behind material with a moisture content as low as 7-10%. Additionally, dewatering screens require minimal maintenance compared to screws and hydrocyclones due to them having fewer moving parts. Dewatering screens are also suitable for high volume operations as they have a high throughput capacity.
Every piece of equipment has its limitations, and dewatering screens are no different. Dewatering screens may not be ideal for operations that are processing very fine materials such as clay or silt-laden feeds. It is also imperative to have the correct size screen and frequency to maintain optimal performance levels.
Sand Washing Plants
Sand Washing Plants perform both washing and dewatering of material. They remove dirt, silt and clay from sand before removing excess water. These plants are used to produce clean aggregates for multiple applications including aggregates, concrete, frac sand and more. Sand washing plants, such as EIW’s Falcon Sand Plant, consist of a sump, pump, hydrocyclone(s) and dewatering screen(s).
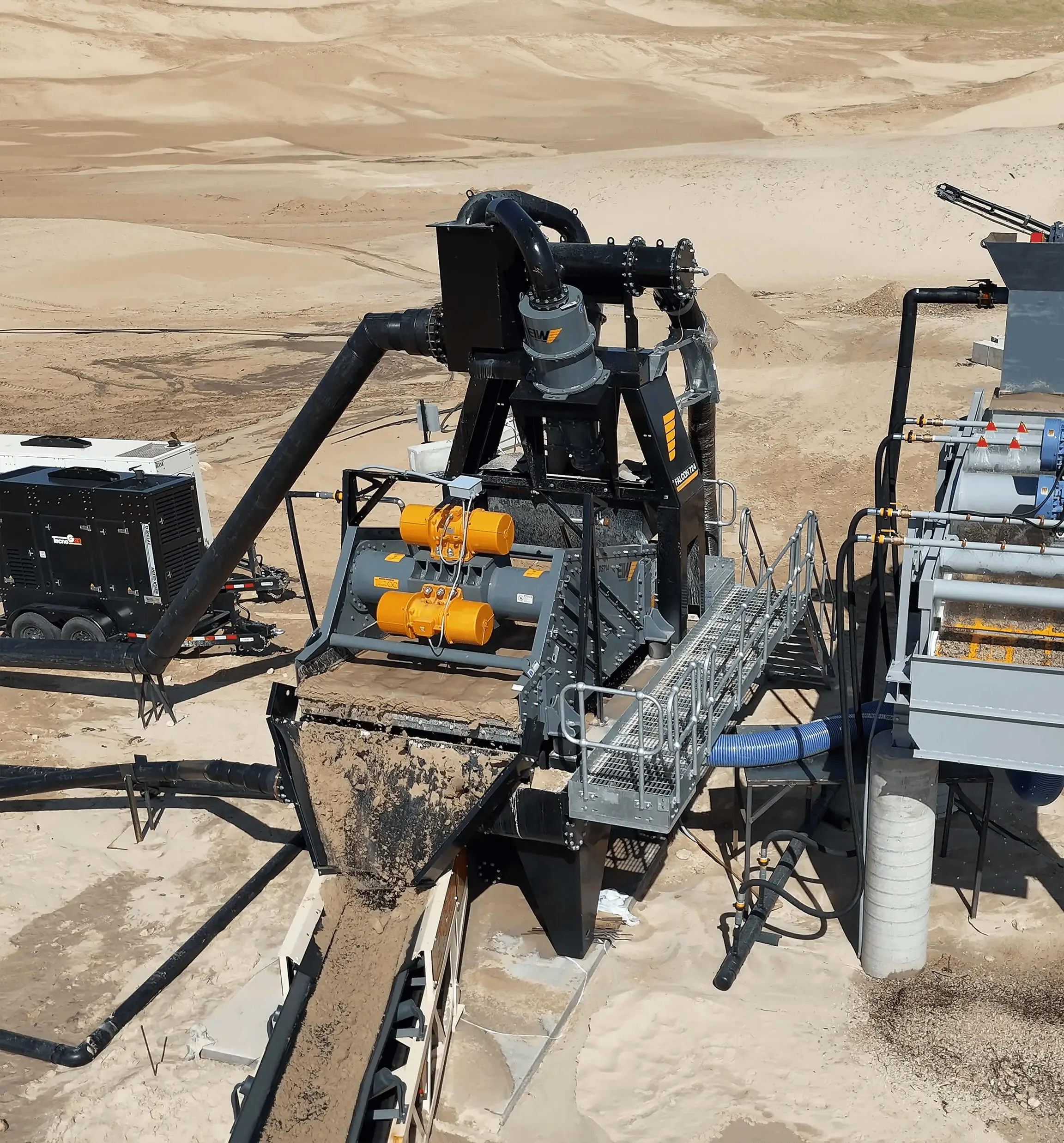
Sand washing plants offer several key advantages that enhance efficiency and sustainability in aggregate processing. Their dual functionality allows them to clean and dewater sand in a single step, streamlining operations and reducing the need for additional equipment. These plants feature high water recycling capabilities, utilizing closed-loop systems to minimize waste and promote sustainable resource management. Additionally, they improve sand quality by effectively removing contaminants such as organic matter and silts, ensuring a cleaner, more consistent final product for construction and industrial applications.
Compared to screw washers, sand washing plants can have higher capital and operational costs. Additionally, some designs of sand plants may be better suited for ultra-fine material recovery.
Fines Recovery Plants
Fines recovery plants, such as EIW’s Hawk Fines Recovery Plant, are designed to capture fine particles that are typically lost in wastewater streams. They consist of a dewatering screen, pump, sump, and hydrocyclones. The hydrocyclones are used to separate the fine particles from the wastewater while the dewatering screen further reduces moisture content. A portion of the overflow is used for sump level control, while the remaining amount is sent to the pond or to additional downstream processing equipment.
One key advantage of fines recovery plants is the ability to recover and use fines as a saleable product rather than waste. These recovered fines can be sold as a byproduct for pond lining or backfill material. This also reduces the amount of solids that are sent to a settling pond and as a result, leads to less time spent cleaning out ponds. Finally, fines recovery plants can be used to prepare waste for water recycling in downstream equipment, which can be beneficial in areas where water is scarce.
Although hydrocyclones have no moving parts, they can often be responsible for performance limitations within a fines recovery plant. Hydroyclone performance is heavily influenced by the size gradation of the feed material, as oversized particles can cause underflow blockages. When even one hydrocyclone in a cluster plugs, untreated material can short-circuit to the overflow and be lost to waste, potentially escalating quickly if multiple hydrocyclones become blocked.
Fine Material Washers
Fine Material Washers are a simple yet effective piece of equipment designed to perform three related actions: washing, classifying and dewatering. Fine material washers perform these actions by the continuous rotation of the spiral conveyor shaft and velocity of the overflowing wastewater acting on the feed material. The rotating shaft agitates the material, providing particle-on-particle attrition and allowing deleterious coatings to be removed from the solids and discharged with overflowing wastewater.
Fine Material Washers are typically used for cleaning and dewatering sand and gravel before stockpiling. They can also be used for removing excess fines from crushed stone or concrete aggregates.
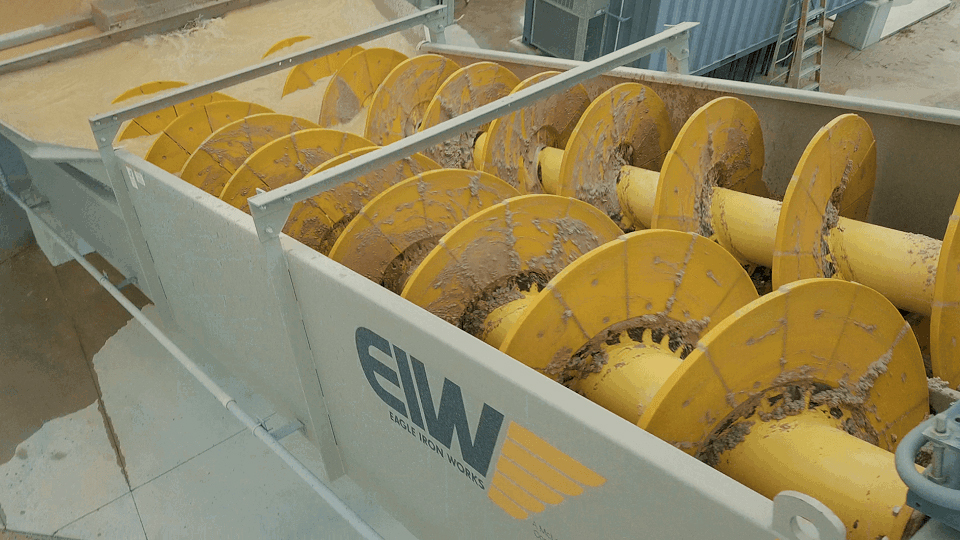
There are plenty of advantages for using a fine material washer as they are suitable for most sand and gravel applications. Fine material washers are a cost-effective and simple option when compared to hydrocyclones or filter presses. They are also easy to operate as they utilize fewer moving parts and require minimal maintenance.
When choosing the right equipment for your operation, consider the following limitations of fine material washers. If improperly adjusted, fine material washers can lead to significant material loss. Additionally, other equipment options may be better suited for handling ultra-fine materials. Lastly, water usage must be carefully managed to avoid excessive waste.
Filter Presses
Filter presses maximize water recovery by separating solids from liquids in a slurry. Although they can be used in a variety of industries, they are mainly used for clarification, dewatering and filtration in liquid-solid applications. Filter presses use a series of recessed plates, covered with filter cloths, to separate solids from liquids in slurry through a high-pressure filtration process. As slurry is pumped into the chambers formed between plates, solids collect on the cloths while filtered liquid exits through designated ports. Once the filtration cycle is complete, the press opens to release the dewatered solid cakes, which are then discharged for further handling or disposal.
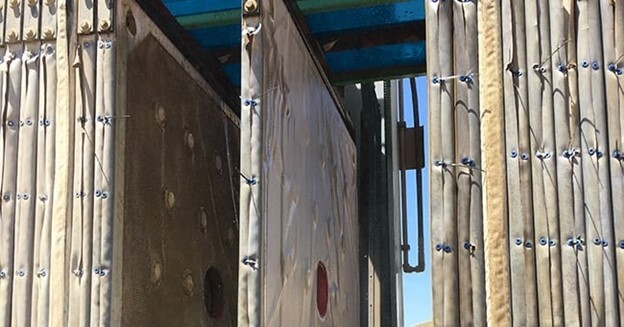
Filter presses are often used in applications that require maximum water recovery and solid waste reduction. This can also include sites with strict environmental discharge regulations. Because of the amount and quality of water recovery, filter presses are also beneficial in areas where water is scarce or expensive.
Filter presses provide highly efficient dewatering and produce the driest material of all equipment options. They also maximize water recycling as nearly all the water is recovered for reuse. Filter presses also reduce sludge volume, allowing for cheaper and easier disposal of waste materials.
Price can be one of the biggest limitations when it comes to filter presses. They have a higher upfront cost than other pieces of dewatering equipment. They also require specialized operation and maintenance. Lastly, they can have slower processing time, which may not be suitable for operations requiring continuous dewatering.
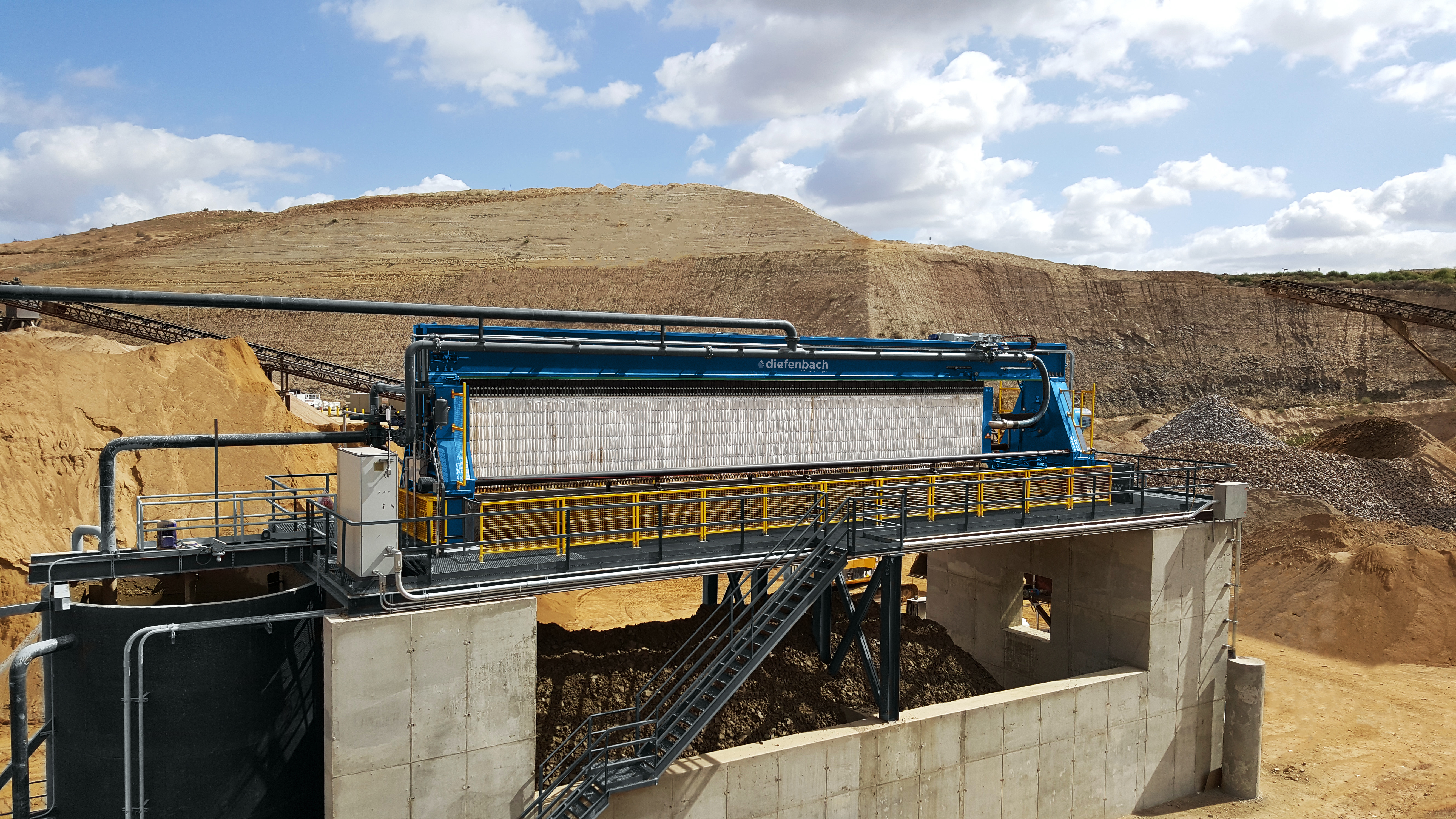
Ultimately, the best piece of dewatering equipment depends on the individual operation and what they are looking to get out of the equipment. To summarize: Dewatering screens are the best option for general moisture reduction. Sand washing plants are a good option for washing and dewatering simultaneously. Fines recovery plants maximize material capture while fine material washers offer a simple and cost-effective option. Lastly, filter presses provide the driest product but require higher investment.
To choose the right equipment for your operation, it is important to consider material type, water recovery goals, production scale and budget. Contact Eagle Iron Works or your local dealer with any considerations and questions, and they can help to select the right dewatering equipment to maximize your efficiency and results.