
What to Know About Aggregate Screening Equipment
Screening is a key part of processing aggregates. It is the sorting of material into different sizes to determine the specification of your material and to ensure you generate a high-quality product. There are two main types of aggregate screening equipment: Inclined Screens and Horizontal Screens.
Each type of screen has its own benefits depending on the application. Before deciding which aggregate screen is ideal for your application, it is helpful to understand aggregate screening equipment basics.
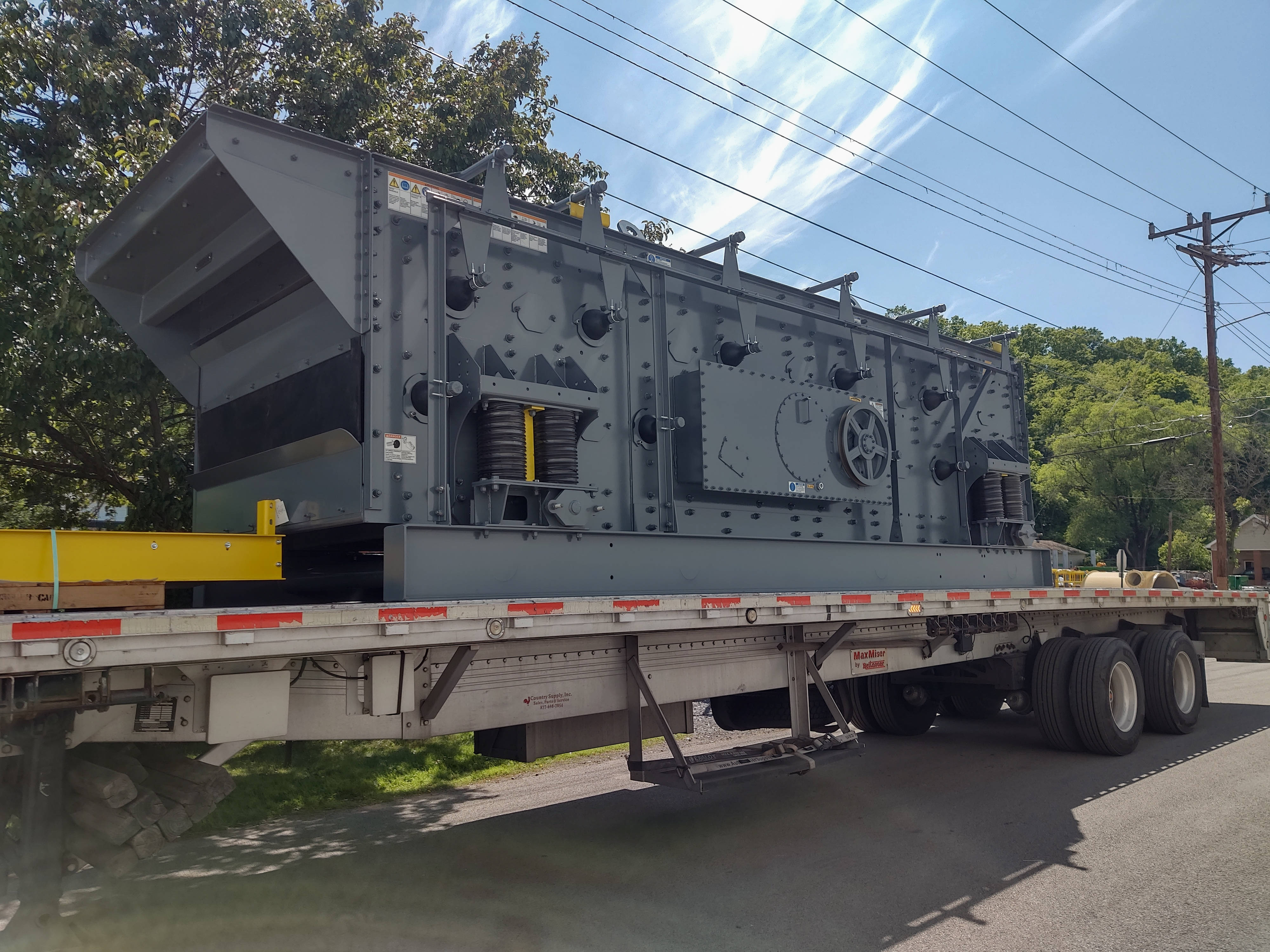
Function of Aggregate Screens
Screening provides two solutions: separating aggregates and/or washing aggregates. Whether you’re separating or washing your aggregates, screening helps create an optimal product.
In a separation application, material is sorted by particle size to ensure a quality product that meets specifications. In a washing application, screens are equipped with spray bars to rinse material after it is processed by a Log Washer or Coarse Material Washer. Screens can also combine these solutions for both separating and washing material in the same machine.
Key Components of Aggregate Screens
Deck: The deck of an aggregate screen is the surface on which the material is conveyed to the discharge point. Multiple decks can be installed to separate material into multiple sizes. Each deck contains screen media with progressively smaller openings.
Screen Media: Screen media allows material of different sizes to be sorted, depending on the size of the openings in the media. Screen media comes in a variety of materials and sizes, including woven wire, rubber and polyurethane.
Shafts and Counterweights: The screen produces motion via shafts and counterweights inside the screen box. Shafts provide different kinds of motion depending on the application.
For example, single shafts create a circular motion, throwing the material higher. Shaft motion can also create straight line throw and oval stroke.
The number of shafts also depends on the size of the screen. The larger the screen, the more shafts required to provide motion.
Spray Bars: Spray bars dispense water over material, cleaning the material as it is sorted. They help remove debris from material before stacking for further processing.
How Screens Work
Material is fed onto the top deck of the screen. The vibrating motor puts the shafts and counterweights in motion, agitating the material and conveying it along the deck. As the material moves, gravity pulls smaller particles down through the screen media, while larger material continues to move across the decks to a discharge point for stacking or further processing.
Important Screening Parameters
The effectiveness of a screen depends on several parameters, including speed, stroke, rotation direction and inclination angle. Here are the basics that help determine the effectiveness of your screening process.
Speed: The speed of the screen’s motion is what allows material to move across the screen deck. It’s important to account for the screen’s stroke when deciding speed. While speed helps move material, too much speed can create unnecessary stress on the equipment.
Stroke: Stroke is the amount of vertical distance that the screen moves. Speed and stroke work together. A typical application for separating coarse material employs a low speed and a large stroke. Fine separation usually employs a high speed and small stroke.
Incline: The degree of the incline can affect the efficiency of an aggregate screen as well as the amount of stratification that occurs during screening. Stratification is when finer particles fall through coarse material.
Larger materials typically require a lower incline to give them time to pass over and potentially fall through the screen deck, while finer particles can easily move across a screen with a higher incline.
Less incline is used in scalping applications of large materials, while more incline is used for finishing applications of small materials.
Inclined Screens vs. Horizontal Screens
Eagle Iron Works supplies two types of aggregate screening equipment: Horizontal Screens and Inclined Screens. While both pieces of equipment have the same purpose, each machine has its own features that make it more suitable for an application. Choosing the right screen for your process is important to achieve an efficient and profitable operation.
Inclined Screens
Inclined Screens are the most popular type of screen for aggregate processing. Installed on an incline between 5 and 45 degrees, Inclined Screens rely on gravity to move material over the screen decks.
Because this type of screen uses gravity to move material across the deck, Inclined Screens have a low stroke, a low G-force and a faster material travel rate.
Using a circular vibratory motion, Inclined Screens lift material to help stratify the material before separation. The incline combined with the circular vibratory motion conveys material down the deck.
Inclined Screens can be used throughout material processing. Before crushing, scalping screens remove fine material from the feed to protect the crusher from wear. In the secondary stage, screens separate material into different sizes for further crushing or stockpiling.
Horizontal Screens
Horizontal Screens operate at zero degrees but can be inclined up to 10 degrees in either direction. They are ideal for low-profile applications that have limited height requirements, making them the best suited for primary screens in portable plants.
As part of a stationary plant, Horizontal Screens are used for most stages of final screening. Horizontal Screens are beneficial for finer screening applications because they provide more accurate particle sizing.
Horizontal Screens require a high G-force since the motion of the machine alone is what conveys material along the screen deck. Because of this high G-force, screen media is less likely to experience plugging, optimizing screening efficiency. Plugging, or pegging, occurs when near-size particles become stuck in screen media openings, reducing screen surface area and the efficiency of the screen.
How to Choose a Screen for Your Application
It’s important to consider a number of factors when deciding what screen is best for your application.
Determine the best size
Sizing your screen is critical to optimize the efficiency of your application. Consider the capacity for your operation and determine your particle size distribution and your required cut point(s).
The size of your screen is dependent on your application and your needs. Discuss with your screen manufacturer to determine the best solution for you.
Pick your screen media
There are various kinds of screen media, with the most used being woven wire cloth, polyurethane screens and rubber screens. Woven wire cloth is the most commonly used due to its durability. It has a 50-70% open surface area, allowing more material through, but can be more easily damaged in abrasive applications.
Polyurethane screens are normally used for wet applications but are suitable for dry applications as well. Opposite to woven wire cloth, polyurethane screens have a longer wear life but less throughput (about 30-40% less than wire cloth).
Rubber screens are similar to polyurethane screens with an increased wear life compared to wire cloth but a smaller open area, limiting chances for particles to pass through. Rubber screens are ideal for coarse and abrasive material in dry applications.
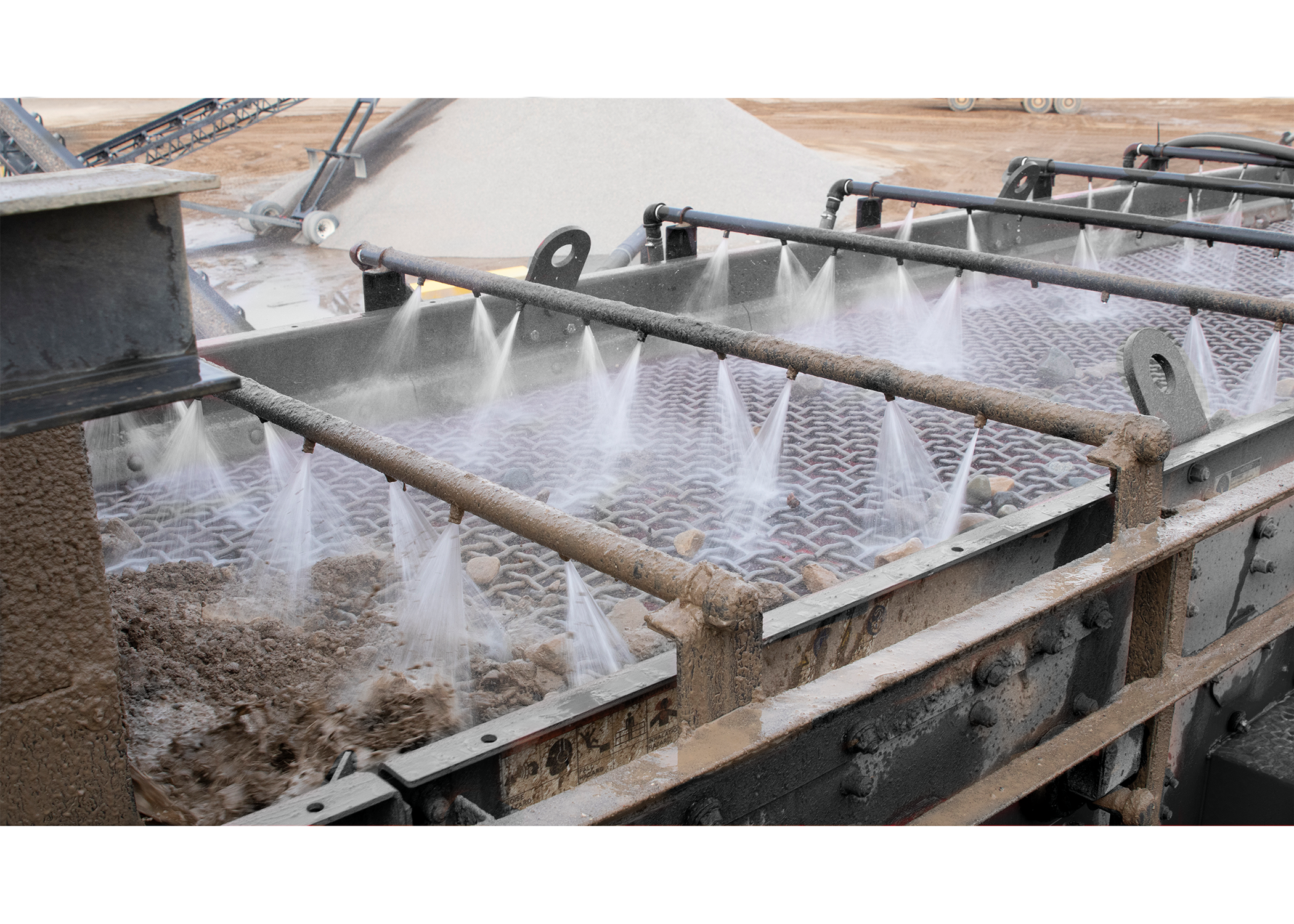
Tips for an Efficient Screening Process
To get the most out of your screening process, here are a few tips:
Determine the best speed for your application
Speed and stroke are crucial to determining your screen’s efficiency. Different combinations of speed and stroke types yield different results depending on the application and material being processed.
It’s important to weigh the pros and cons of changing your screen’s speed. Increasing speed increases the screen’s carrying capacity, material acceleration and travel rate, increasing screening efficiency.
However, increasing speed increases wear and stress on the machine, decreasing bearing life.
Determine the best stroke type for your application
There are different types of motion produced by shafts and counterweights inside a screen box. Different types of motion, or stroke, affect screen efficiency and effectiveness.
Circle throw is typically used for Inclined Screens and requires low energy due to the incline of the screen in combination with gravity. It can be configured with a single or dual shaft.
Linear or straight line stroke, also called reciprocating stroke, uses dual counter rotating shafts and is common on Horizontal Screens. Straight line stroke is efficient and accurate; however, plugging in screen openings can occur.
Unlike a circle throw, reciprocating stroke doesn’t throw the material in the air and uses a shuffling motion, increasing the chances of plugging.
Oval stroke is the most efficient and accurate of the three stroke types. It is typical on triple-shaft Horizontal Screens. Its high energy loosens fines and reduces the chances of plugging on screen media. Plugging occurs when particles become stuck in screen media openings, reducing screen surface area and the efficiency of the screen.
Feed considerations
Some material is screened better than other types. Slabby, jagged, crushed material doesn’t separate as easily or accurately as cubical products, sand or gravel. However, any material can be screened. Sticky materials can also create blinding of the screen openings, resulting in loss of screening efficiency. When fine particles stick to the surface media from moisture, blinding occurs. Consider the type of crusher you want to use for your operation to provide an ideal feed for screening.
How do I Optimize My Operation?
Optimizing efficiency
There are multiple methods for optimizing your screen’s efficiency. Changes to consider include lowering the incline angle of the screen, changing the type of screen media to one with more throughput, considering wet screening and trying different stroke and speed combinations.
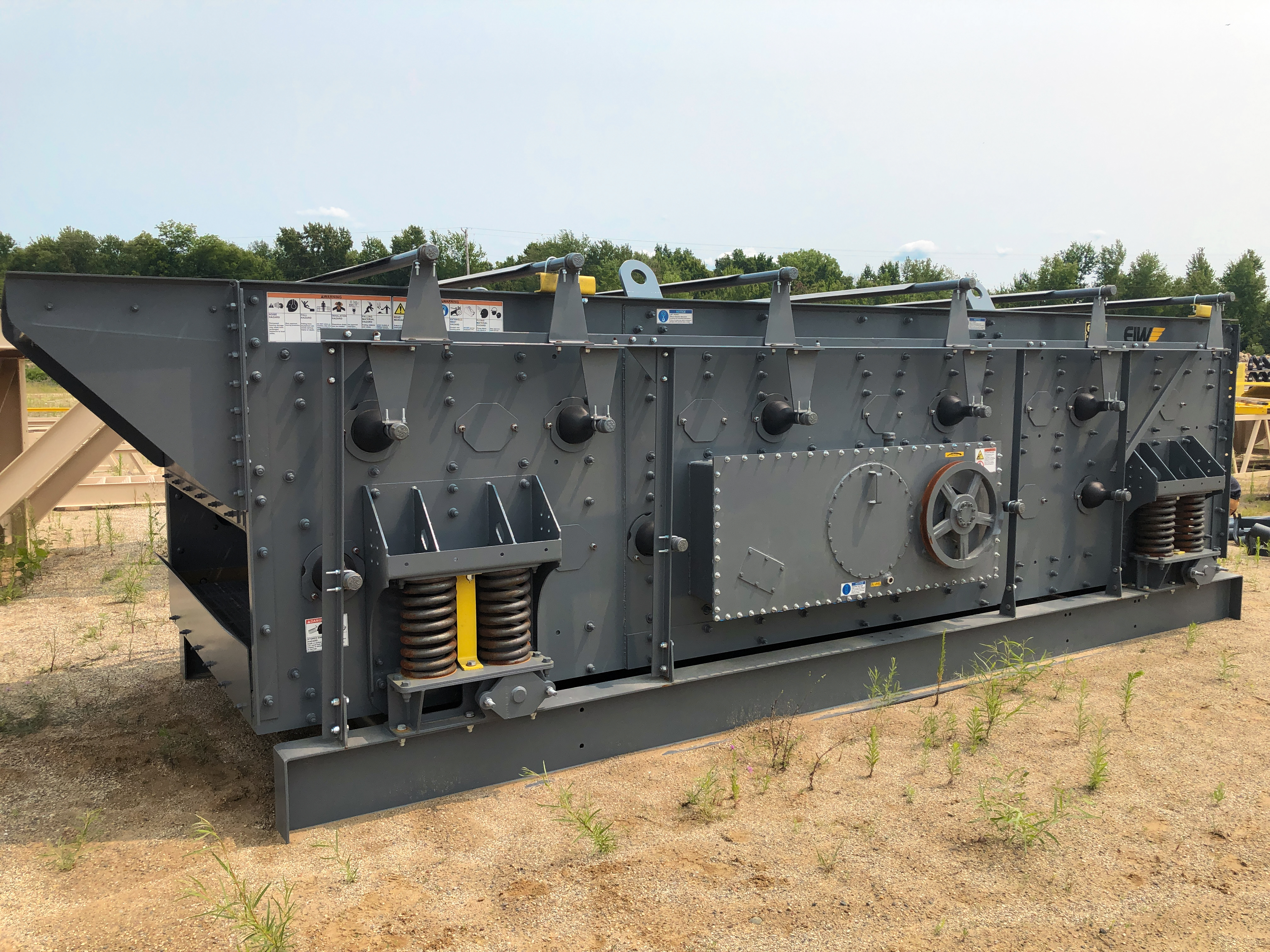
Wet screening not only washes the material as it is conveyed along the screen deck, but the water from the spray bars essentially blasts the material through the screen media openings. Wet screening increases the chances for material to be sorted and decreases the chances of plugging.
Improving stratification
Stratification occurs when fine material falls through coarse material on the screen deck due to the motion of the screen. Stratification is important for effective screening and separation. To improve stratification, you can decrease the material feed rate, increase the angle of incline or try wet screening.
Decreasing the material feed rate and increasing incline allows material to be more easily distributed across the deck, increasing the chances of stratification.
Improving probability of separation
To improve probability of separation for your operation, you can reduce material feed rate, decrease travel rate, change to a wet screening operation or try a different type of screen media.
Decreasing feed rate and travel rate help slow down the material on the screen, allowing for more time to separate. Wet screening helps blast material through the screen media openings to increase separation.
Why Eagle Iron Works?
Eagle Iron Works provides tough, durable equipment for every step of aggregate processing, from Washing and Classifying to Tailings Management and Water Recycling. Eagle Iron Works manufactures designs for every customer according to their needs.
Eagle Iron Works manufactures both Horizontal and Inclined Screens, ranging from 4’ to 12’ wide and 6’ to 32’ long. With years of experience, Eagle Iron Works can provide the best screening solution for your application.