
Tips for Classifying Tank Calibration
Classifying Tanks are commonly used for removing silts, retaining fine mesh sizes, and classifying sand for many construction grade specifications. Classifying Tanks, also known as Water Scalping Tanks, are also used to remove large amounts of excess water such as in suction dredging mining operations and to make multiple products from a single feed.
Eagle Iron Works Classifying Tanks feature a valve bridge with six to 11 valve stations that consist of a sensing device and up to four hydraulic cylinders that operate valves at the bottom of the tank. When a sand slurry enters the tank, the larger particles settle out in the first stations, with successively smaller sizes settling out in the remaining stations. When the sand reaches a level that stalls the sensing paddle in each station, the valves discharge into separate collecting-blending flumes below the tank. The valves discharging fine and coarse sand fractions are controlled by a process controller and channeled to the dewatering equipment downstream of the Classifying Tank.
To improve efficiency and classification, Eagle Iron Works recommends a Rising Current Classifier option in the first three stations of the Classifying Tank. This keeps the lightweight (smaller) sand particles in suspension while allowing the heavier (larger) particles settle out in the coarse end of the tank. The addition of a Rising Current Classifier allows for better control over final product gradations.
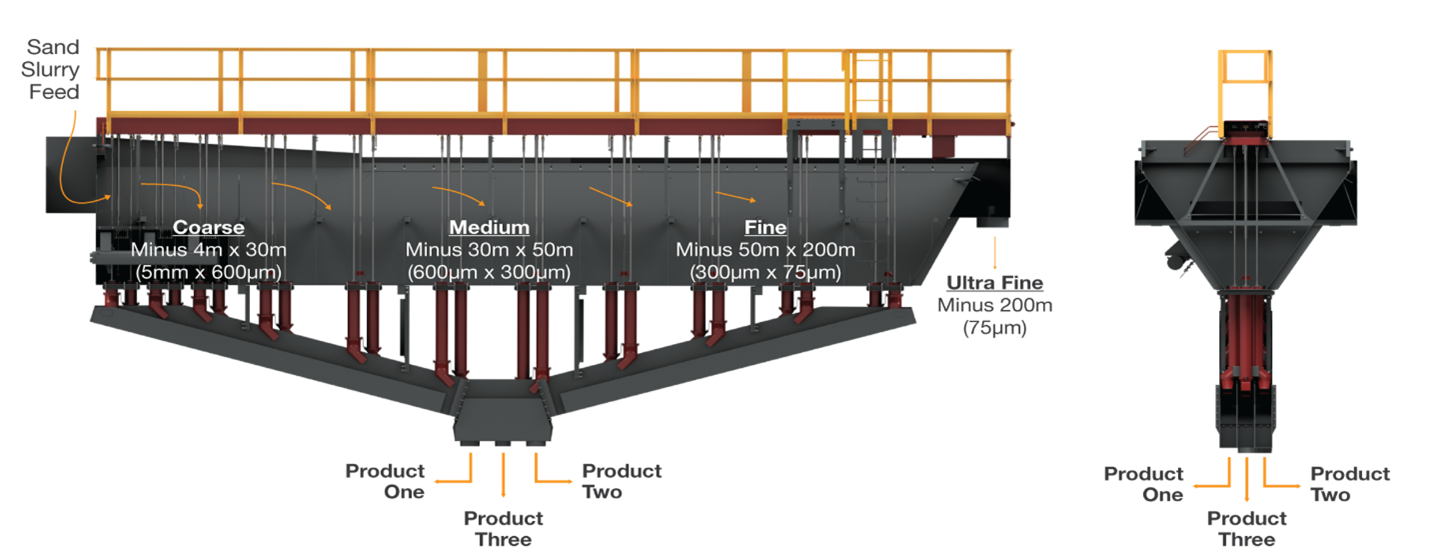
The type of control system used to operate the Classifying Tank is also important for efficient classification and spec sand production. Classifying Tank control systems can help to eliminate time consuming tasks such as manually adjusting splitter gates used on early Classifying Tanks. Some control systems perform complex calculations allowing maximum production yields of construction spec sands. Based on sand accumulation in the tank, the control system will determine which valve to open in that station of the tank. Once product specifications are achieved, the control system will continue to produce in-spec material when inputting periodic product pile gradations into the control system’s software program.
Why is Classifying Tank Calibration Important?
Calibrating and maintaining a Tank should first involve making sure that all the electrical and mechanical components of a Sand Classifying Tank are functioning properly. Calibrating a Classifying Tank is important to ensure that the products, typically construction-grade sands, are in-spec. Since many of the materials being processed go into state DOT highways, keeping the system calibrated is important to ensure you get the right sizes and gradations in these products.
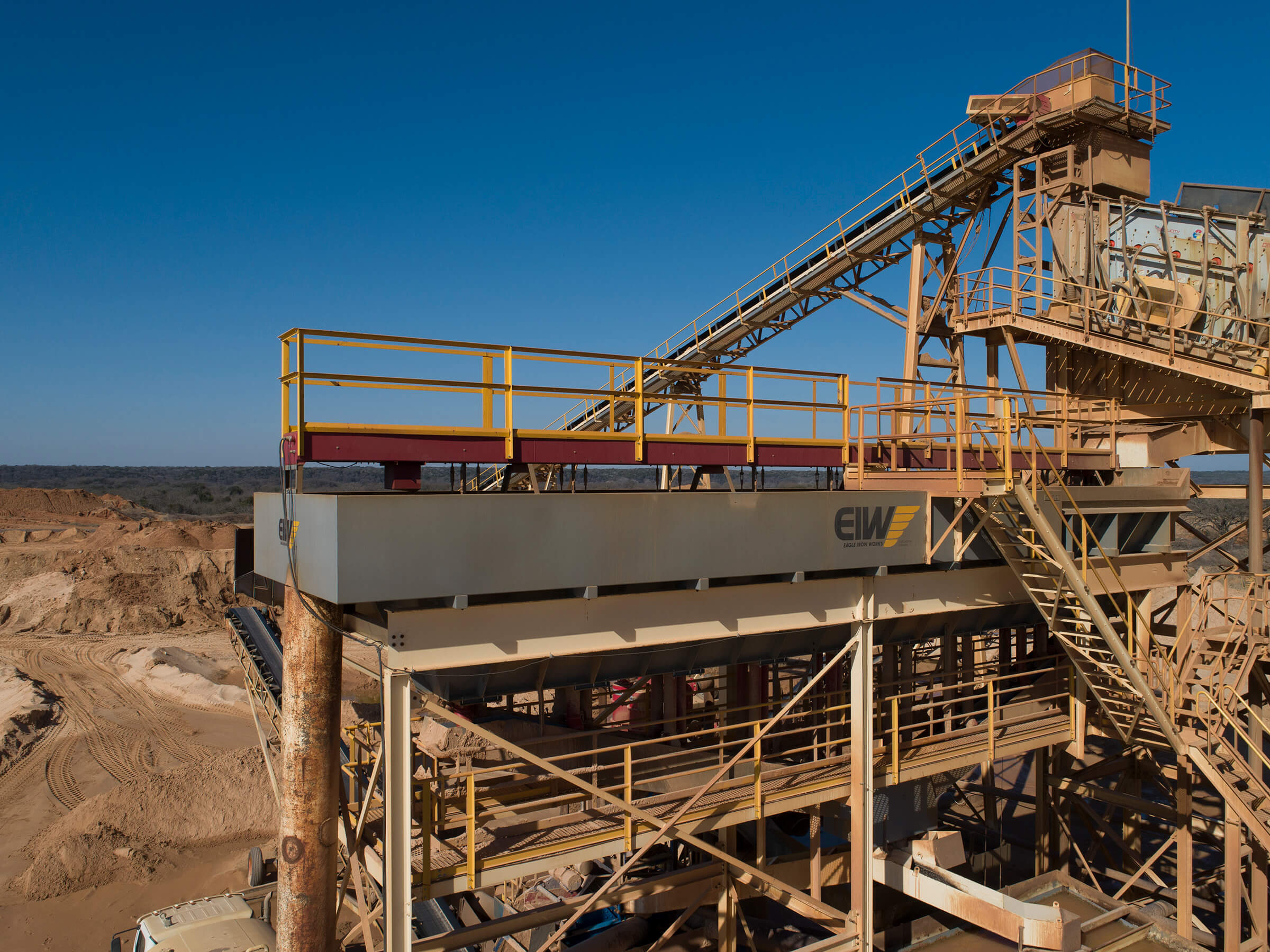
How to Calibrate a Classifying Tank
The process of calibrating a Sand Tank involves ensuring that the valves are adjusted correctly. The valves that move up and down in each station must be adjusted to a certain depth to allow coarser material to flow through. If the valves are not set correctly, they may not allow a high volume of sand to quickly discharge through the valve seat, which might create flow issues.
To best optimize your Sand Tank, an operator should review the tank’s electrical system. Switches on older units located in the valve bridge or older electromechanical controllers can fail. It is important to ensure these are functioning properly.
Regardless of the control system used on a Classifying Tank, adjusting the unit — or ‘dialing it in’ — is always recommended. The most important detail is to make sure that the sand discharging from the first three valve stations is as coarse as possible. Ideally, the sand discharging from the first two and, if possible, first three valve stations should be 10% or less passing 50 mesh or 300 microns. If sand discharging from these valves has a higher amount of minus 50 mesh, adjustments to the rising current classifier manifold valves need to be made to provide more uplifting water by volume. This water can be provided by a fresh water source connected to the rising current classifier manifold or the recirculating pump if it was supplied.
Additional changes to the rising current classifier section of a Classifying Tank can include adjusting the slot opening on top of each rising current chamber as well as positioning and leveling the side and end weirs to the optimal position.
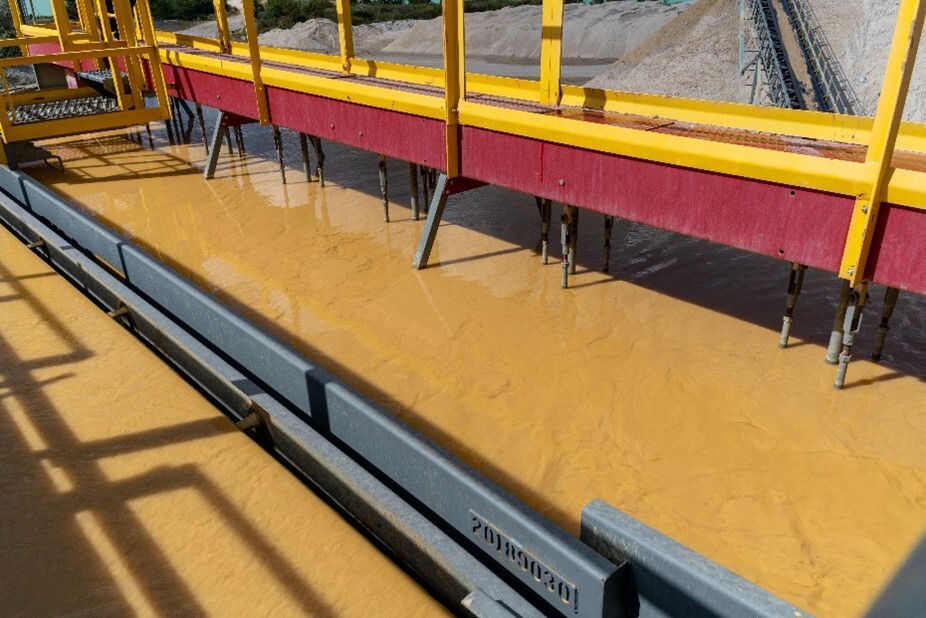
When Should a Classifying Tank be Calibrated?
Classifying Tanks typically need to be calibrated when there is a major change in feed material or if a mechanical or electrical component has changed. If there is a known change in the particle size gradation of the sand feed or if adjustments to a Classifying Tank’s controller make it difficult to maintain production of a specification construction sand, sampling the sand discharging from stations one, two and three and making a gradation analysis of each sample would be recommended. If the amount of sand passing 50 mesh or 300 microns is higher, adjustments or changes to the rising current classifier section need to be made. Depending on the sand feed gradation, it may be necessary to make a change to the equipment feeding or preceding the Classifying Tank if there is an excessive amount of plus 16 mesh or 1.18mm coarse grit in the feed.
Classifying Tank Control Systems
Most all Classifying Tanks made since 1970 have been supplied with some type of control system to operate the valves. Control systems have evolved over the years with the advance of technology, from using electro-mechanical timers to programmable logic controllers (PLCs) to computer controlled/monitored systems having software developed specifically for maximizing the yields of spec sand production. The current control systems from Eagle Iron Works include the Digital DIALSPLIT and the Mark X.
Digital DIALSPLIT
The Digital DIALSPLIT is the latest base Classifying Tank control system from Eagle Iron Works. It allows you to control your operation with percentage-type settings, making for quick and easy product control. The advanced memory system allows you to save up to 12 recipes to reference and change to at any time.
The main advantage of this control option is that it eliminates the time-consuming job of manually adjusting splitter gates or ‘dials’ on older Classifying Tank control systems, which could be as large as refrigerators. This control system is easy to understand and operate. A touchscreen HMI allows simple changes to the valve openings for each station, which corresponds to the number of valves and cells in the tank. Each cell can produce a controlled product, with one cell yielding a residual product. For existing Classifying Tanks using the older control systems, a replacement Digital DIALSPLIT panel can be supplied. In certain older panels, replacement componentry has been discontinued if parts need to be replaced.
Mark X
The Mark X software is an add-on feature to the Digital DIALSPLIT system. This software was developed to meet the needs and demands of many EIW customers. The process of making sand with a percentage-type control system is not the most efficient for some producers. With a varying sand feed, an operator using a percent-type control system frequently has to check feed gradations and then manually make adjustments. If they make an adjustment that doesn’t work, their product may be out of spec.
The software behind Mark X was developed to automatically make changes for the operators and to calculate the percentages so that the customer can stay in spec more consistently. This automatic process can save customers time and allow them to perform other tasks. With manual adjustment, you may not catch that the product is going out of spec. Because the Mark X system will detect if the product begins to go out of spec and adjust on its own, the cost of lost material is decreased.
In applications where the feed is constantly changing, it is hard for operators to keep their product in spec. The Mark X software will automatically adjust to keep the product in spec, minimizing lost production. Sampling product piles periodically is still necessary to ensure production of in-spec sands.
The auto-calculations were the main driver for developing the Mark X, along with ensuring that the software could complete these high-level calculations accurately. Several features of the Mark X software have been developed as a result of conversations with customers who are using the software directly.
How does EIW’s Mark X Classifying Tank Software help a Classifying Tank user?
EIW’s Mark X software is designed to maintain a consistent specification sand discharging from a Classifying Tank. After the Classifying Tank is adjusted or calibrated for the most efficient production of two construction-grade products, your sand will remain in spec. The software performs the complex calculations necessary to achieve a maximum yield of spec sand. Periodically updating the software with your product pile quality control gradation data allows the tank’s station percentages to automatically adjust accordingly, permitting tight tolerances for typical construction sand specifications with moderate changes or swings in a sand feed.
What are the benefits of using the Mark X Software?
Mark X keeps products in spec, minimizes lost product or waste and frees up other resources. The Mark X software has built-in production tracking and keeps track of daily yield, tons produced and tons per hour. This software shows much more production-related data than other software. Mark X also increases productivity and throughput of a Classifying Tank. It frees up manpower that could be better spent doing other things around the site.
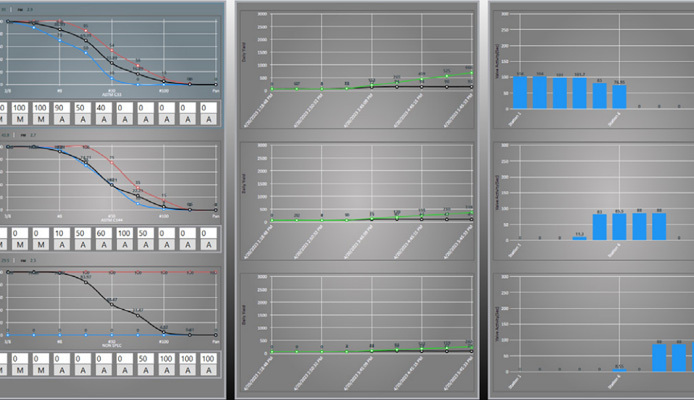
How does someone get their existing Classifying Tank fitted with Mark X?
To convert most any brand of Classifying Tank to using the Mark X add-on software with an EIW Digital DIALSPLIT control system, contact EIW. The Mark X software is also available as a replacement for older versions such as Mark V and VI control systems on existing EIW Classifying Tanks.
With the remote-in ability that comes standard with the Mark X control system, lifetime software and troubleshooting support are provided. Contact your Eagle Iron Works dealer for more details, pricing and to learn more about how the Mark X can benefit your operation.